KISTLER
Solutions to improve power quality
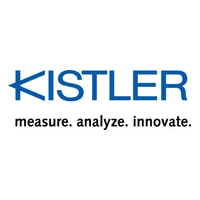
The company
The Kistler Group produces both complex measuring systems for the R&D sector and measuring systems for assembly that guarantee high quality in production, offering a wide range of sensor types. It also offers complete acquisition systems for a wide range of assembly, testing and development tasks. It also offers high quality tools for tightening, component analysis and calibration benches for torque spanners and screwdrivers.
- Electric presses for joining and assembly;
- Rotary (strain gauge) and static (piezoelectric) shaft and flange torque transducers;
- Measurement and acquisition of piezoelectric force transducers and strain gauges (load cells);
- Piezoelectric strain transducers;
- Control electronics; monitoring of x/y curves; torque/angle.
ELECTRIC PRESSES AND ASSEMBLY SYSTEMS (PROCESS)
Electric presses and electric assembly systems are systems for pressing and joining, which can be used for force/displacement process control, process quality assurance, product, profitability and operational reliability. They provide a long list of advantages: cleanliness, thanks to the absence of hydraulic oil; low complexity of on-site installation and space saving; cost reduction during assembly and maintenance; low energy consumption. Kistler offers a very wide range of presses, each one designed for a specific use. They can be divided into different families according to features and functionality:
- NCFT electric presses have an integrated electrical force sensor with measuring ranges of 0.05 ... 1.5 KN. These instruments can be used for clean room applications and the processing of products in the medical sector. A further feature is the wireless signal, which allows high measurement accuracy.
- The NCFH electric presses save enormous space, thanks to the hollow-shaft motor and integrated piezoelectric force sensor. The measuring ranges vary from 1... 60KN and two different sizes are available. These presses operate at high speeds and are therefore suitable for dynamic joining processes.
- The NCFS electric presses have an integrated piezoelectric force sensor and two predefined measuring ranges of 25 and 15KN. These presses have a particularly slim design that allows them to be used in even the tightest of spaces. They are ideal for automated production facilities due to their rigid design, which allows for extremely precise indications.
- The NCFS electric presses type 2152B... consist of a robust construction with integrated piezoelectric force sensor for working in both compression and tension and is ideal for use in automated production systems. Its special design allows for narrow press station spacings.
- NCFE electric press es are compression-only presses. The force they can generate ranges from 2 KN to 80KN depending on the model.
- NCFN electric presses with strain gage technology are available for nominal joint forces of 30, 60, 100, 200 and 300 KN. They can be used in automated as well as manual production plants. They are also available with safety brake and a customised design is available on request.
- The new NCFC electric presses splice module type 2163A... with integrated strain gauge force sensor for splice forces of 55 KN (size 1) and 80 KN (size 2) barycentric design.Weight-optimised, ideal for robot applications.
- NCFR electric presses are designed for joining processes and rotational movements
More specifically, the most popular Kistler press models are as follows:
Request technical documents for this model
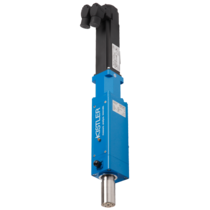
Kistler 2157B electric press
Request technical documents for this model
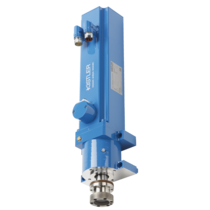
Request technical documents for this model
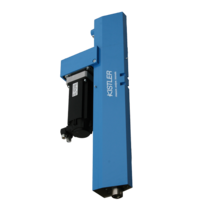
Kistler 2152B press
Request technical documents for this model
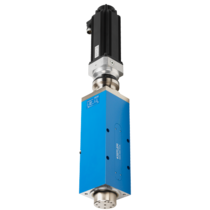
Kistler 2153A press
Request technical documents for this model

Electric press 2162A
Request technical documents for this model
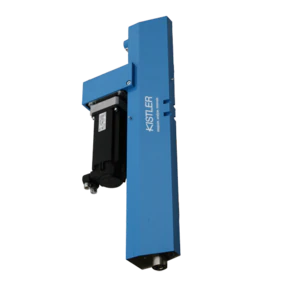
Electric press 2152B
Request technical documents for this model
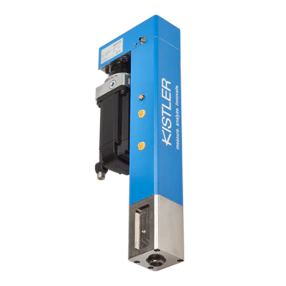
Electric press 2163 A
Request technical documents for this model
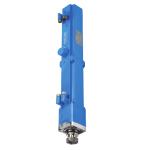
Electric press with torsion movement 2161A
Monitoring systems and accessories
Request technical documents for this model
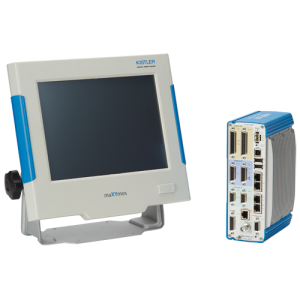
MaXYmos NC 5847B
Request technical documents for this model
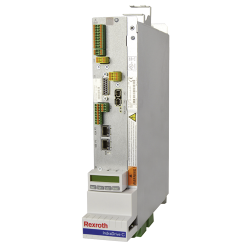
2180 Indra Drive for Kistler Electric Presses
TORQUE MEASUREMENTS: ROTARY TORQUE TRANSDUCERS AND PIEZOELECTRIC STATIC TORQUE TRANSDUCERS
The torque transducer is a measuring instrument used to measure torque, an important mechanical quantity for many applications. Measuring torque with high accuracy, especially on rotating parts, is essential to further improve the efficiency and performance of motors, engines and for industrial process control. Kistler's range of torque transducers includes shaft, flange and non-rotating torque transducers for measuring reaction torque.
TORQUE SHAFTS
Request technical documents for this model
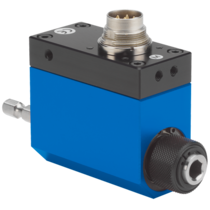
Kistler 4501 Shaft Torque Meter
Request technical documents for this model
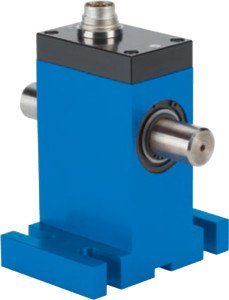
Kistler 4502 Shaft Torque Meter
Request technical documents for this model
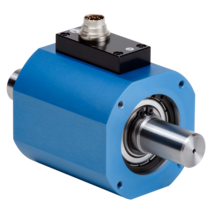
Kistler 4520 Shaft Torque Meter
Request technical documents for this model
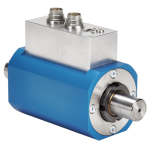
4503 B KISTLER TORQUE TRANSDUCER
Coupling joints for torque shafts
Couplings are important accessories for torque transducers. They are used as compensation components for parasitic loads due to alignment errors. In order to enable the torque transducer to achieve very low measurement uncertainties, Kistler offers a range of couplings suitable for many installation variants. The use of such compensation components not only increases the accuracy of the transducer but also protects the components connected to it from wear.
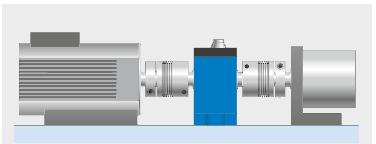
Request technical documents for this model
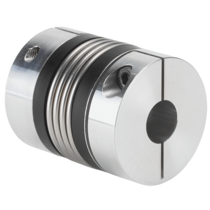
Kistler 2301 coupling for torque shafts
TORQUE FLANGES
Strain gauge torque flanges are ideal for those with limited space. They take up less space and are easier to install. Torque flanges can be fitted with couplings to connect the main shaft to the sensor and the sensor to the application.
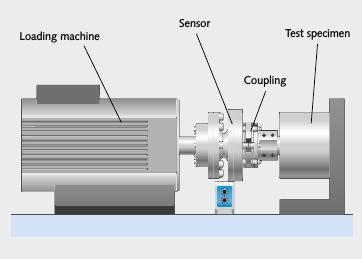
The following models belong to this category:
Request technical documents for this model
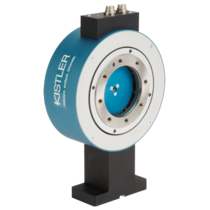
Kistler 4510 torque flange
Request technical documents for this model
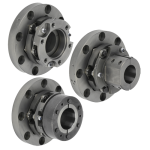
Coupling joints 2304A
Request technical documents for this model
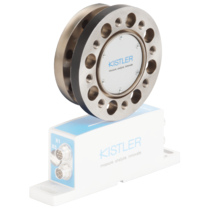
Kistler 4550 A 4551 A rotor
Request technical documents for this model

Kistler stator 4541 and 4542
Request technical documents for this model
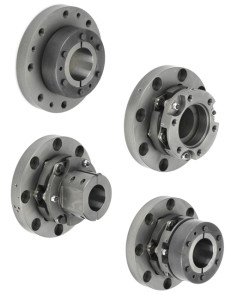
Kistler 2300 and 2305 couplings
MULTI-COMPONENT FORCE AND TORQUE SENSORS
Multi-component force and torque sensors have pairs of longitudinally cut quartz rings that measure the force acting on the sensor. Each pair of rings measures one of the two shear components: longitudinal shear and transverse shear. These sensors are usually mounted in groups of three or four and are suitable for both 3-component force measurement and 6-component force torque measurement.
TORQUE TRANSDUCERS
Static torque transducers are easy to install and are particularly suitable for rapid measurement. They detect even small movements in the sensor axis in both directions of rotation. They are suitable for measuring reaction torques with high dynamics and high bandwidth even under quasi-static conditions (fractions of Hertz), for torque adjustment, spanner calibration, for measurements on clutches and electric motors and for testing rotary measuring switches. Kistler models in this category are:
The following models belong to this category:
They allow measurement of torque on the axis for spring torsion tests, tests on clutches and electric motors, tests for rotary controls. These sensors are pre-loaded and calibratable.
Request technical documents for this model
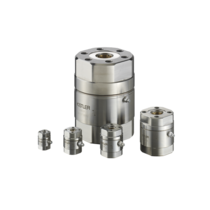
Kistler torque transducer series
They are particularly suitable for example for examining the correlation between drilling torque and breaking force for PCBs, for measuring torque and for screwing processes and the like.
Request technical documents for this model
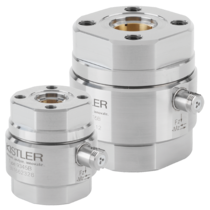
Kistler 9345B multicomponent sensor
CONTROL SOFTWARE
Request technical documents for this model
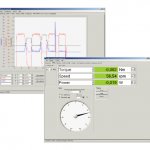
4706A control software
FORCE MEASUREMENTS: PIEZOELECTRIC LOAD CELLS
In recent years, force transducers have reached a high technical standard. The transducers gain part of their high accuracy through improved calibration possibilities. The measurement accuracy of a force transducer depends to a large extent on the state of installation. Unfavourable installation conditions not only have a negative effect on measurement accuracy, but also on the dynamic properties of the measurement chain and immunity to electromagnetic fields.
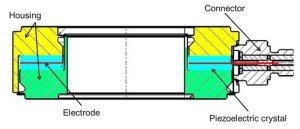
I piezoelectric sensors consist of two crystal disks with a foil electrode between them. When force is applied, an electrical charge is generated that can be measured by a charge amplifier. The charge is proportional to the force applied. Given their principle of operation, these sensors have a drift of 1N/minute while the measurement chain is in operation they show very small deflections when force is applied, thus offering high stiffness. This results in a high resonance frequency which, in principle, is very favourable for dynamic or quasi-static applications. Further advantages of these sensors are: a high operating temperature range high operating temperature range (-196°C; +700°C) and a easy signal summation for sensors mounted in parallel.. All transducers are made of stainless steel and are suitable for use in harsh industrial environments with stringent operational requirements. They are maintenance-free and can be installed in locations that are difficult to access. A further significant feature of piezoelectric technology is the possibility of calibrating and programming different measuring ranges due to the high accuracy. fractioning can be avoidedIt is possible to avoid fractioning, i.e. to use one sensor instead of two or more sensors with different measuring ranges, thus ensuring the most suitable full scale,simply by using the charge amplifier.
These sensors can be to be calibrated o already calibrated. Force washers can be used on both bolts and screws, so the inside diameter of force washers usually corresponds to the outside diameter of metric threads. The resulting force shunt from the bolt or screw on which the force washer is used acts as a spring element in parallel, thus reducing the sensitivity of the system. In this case, a value of approx. 10% should be expected. The force washers to be calibratedThe force washers to be calibrated cannot be calibrated at the factory and calibration is always essential. To ensure good reproducibility, it is essential that the force washer is pre-loaded. The amount of pre-stressing depends on the nominal (rated) force of the sensor and the force to be measured; when the force washer is 50% pre-stressed, it can withstand the maximum bending moments. Ideally, the pre-stress should be such that the sum of the pre-load force and the operating force is on average 50% of the washer's nominal force. This recommendation is particularly important for piezoelectric force washers. The calibrated force washers (load washers) have a high degree of protection and are supplied ready to install, offering the same advantages as strain transducers in this respect; they are therefore preferable pre-loaded and calibrated to uncalibrated washers. Furthermore, as with other piezoelectric transducers, force washers offer sufficient sensitivity to be almost independent of their nominal (rated) force.
The models
Request technical documents for this model
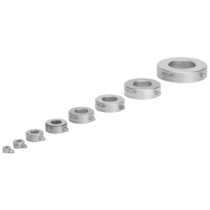
Kistler 9001 piezoelectric load cell
Request technical documents for this model
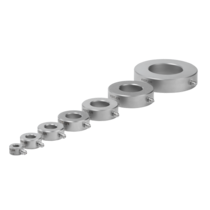
Kistler 9101 Piezoelectric load cells
Request technical documents for this model
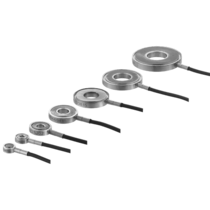
Kistler 9130 Piezoelectric load cells
Request technical documents for this model
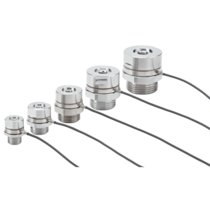
Kistler 9130 Piezoelectric load cells
Request technical documents for this model
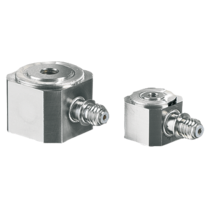
Kistler 9313 Piezoelectric load cells
Request technical documents for this model
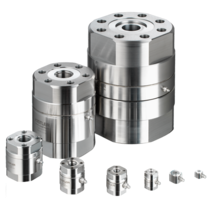
Kistler 9393 Piezoelectric load cells
Request technical documents for this model
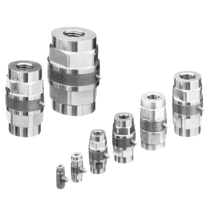
Kistler 9301C Piezoelectric Load Cells
Request technical documents for this model
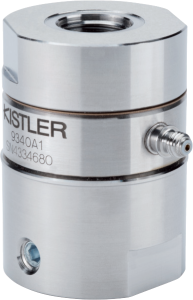
Kistler 9340A Piezoelectric cell
Request technical documents for this model
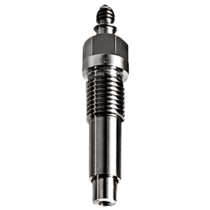
Kistler 9203 piezoelectric load cells
Request technical documents for this model
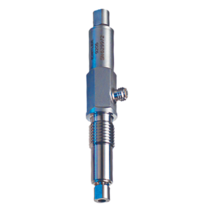
Kistler 9205 Piezoelectric load cells
Request technical documents for this model
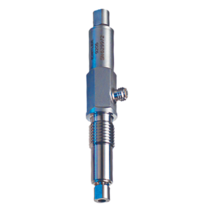
Kistler 9207 Piezoelectric load cells
Request technical documents for this model
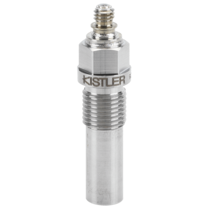
Kistler 9217 piezoelectric load cells
Request technical documents for this model
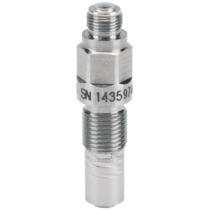
Kistler 9215A piezoelectric load cell
TRIAXIAL LOAD CELLS
Piezoelectric triaxial load cells are sensors capable of measuring a dynamic or quasi-static force in the 3 directions x, y, z. They are characterised by an extremely accurate measurement regardless of the point of force application, a wide usable frequency range and a compact design. They are characterised by a highly accurate measurement regardless of the point of force application, a wide frequency range that can be used and a compact design. These sensors are used to measure shear force during machining, impact forces in crash tests, friction forces and vibrations, but also forces acting directly on products.
Request technical documents for this model
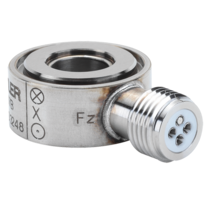
Kistler 9017 Triaxial Piezoelectric Load Cells
Request technical documents for this model
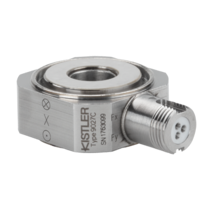
Kistler 9027 Triaxial Piezoelectric Load Cells
Request technical documents for this model
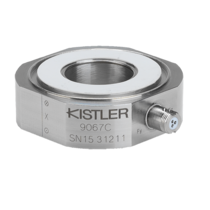
Kistler 9067 Triaxial Piezoelectric Load Cells
Request technical documents for this model
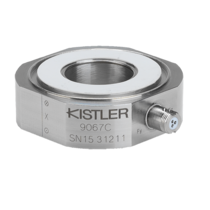
Kistler 9067 Triaxial Piezoelectric Load Cells
Request technical documents for this model
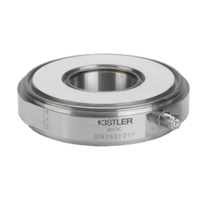
Kistler 9077 Triaxial Piezoelectric Load Cells
Request technical documents for this model
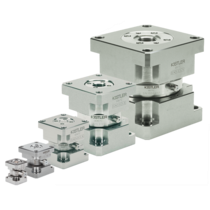
Kistler 9327 Triaxial Piezoelectric Load Cells
FORCE MEASUREMENTS: STRAIN GAGE LOAD CELLS
Load cells with strain gauge technology always include a spring element to which force is applied. This force causes minimal deformation of the spring element. Strain gauges installed at suitable points are lengthened or shortened, and their resistance changes accordingly. At least four strain gauges are connected together to form a Wheatstone bridge circuit. By supplying the measuring bridge with a voltage, the resulting output voltage is proportional to the applied force. Sensors based on strain gauges show almost no drift and are therefore particularly suitable for long-term static monitoring tasks, e.g. weighing. In principle, transducers for small forces are soft spring elements and the resonance frequency of the transducers is correspondingly low. These sensors allow high-precision static calibration and the spring elements can be designed to achieve optimum reproducibility.
Request technical documents for this model
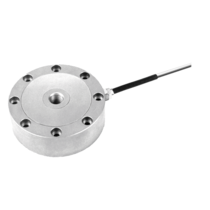
Kistler 4576 strain gauge load cell
Request technical documents for this model
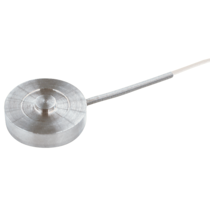
Kistler 4577 strain gauge load cell
Request technical documents for this model
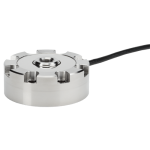
Kistler 4578 strain gauge load cell
Request technical documents for this model
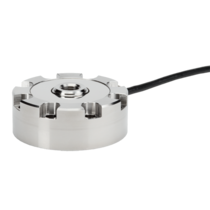
Load cell 4579
Request technical documents for this model
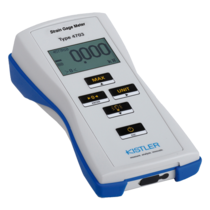
Kistler 4703 portable device for strain gauge load cells
FORCE MEASUREMENTS: SHEAR AND DEFORMATION
Piezoelectric shear load cells are quartz sensors with an extremely flat design, capable of measuring dynamic and quasi-static shear forces. Characterised by extremely small dimensions, high stiffness and maximum resolution, they are ideal for installation in mechanical structures with limited space.
Piezoelectric strain gauge load cells are particularly sensitive sensors that are also suitable for measurements on moving parts. They are suitable for indirect force measurement on mechanical presses, machine tools, high-speed production machinery or assembly units.
Download the technical documents for this model
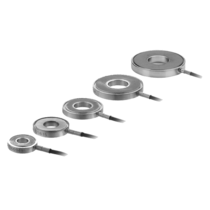
Kistler 9143 piezoelectric shear load cells
Download the technical documents for this model
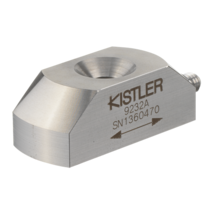
Kistler 9232 piezoelectric deformation load cells
Download the technical documents for this model
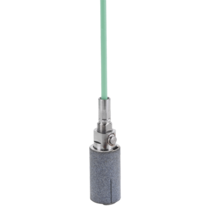
Kistler 9241 Piezoelectric load cells
Download the technical documents for this model
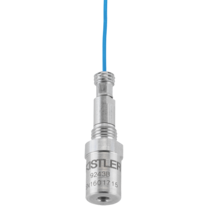
Kistler 9241 Piezoelectric load cells
ANALYSIS: PROCESS MONITORING INSTRUMENTATION
The MaXYmos is a state-of-the-art monitoring instrument for visualising and evaluating joining and press-fit processes. They are therefore designed for measuring, monitoring and testing processes as well as for testing products and materials. They allow fast elimination of waste from the process, improving the quality of the product and the process itself.
The MaXYmos can therefore be used for monitoring Force/Displacement; Torque/Angle; Pressure/Time; Force/Torque in complex assembly and product testing applications and with powerful evaluation techniques, a wide selection of connectable sensors, an unlimited choice of fieldbus types, it offers a range of useful process monitoring functions that guarantee 100% quality in testing and assembly.
Kistler offers two models:
Request technical documents for this model
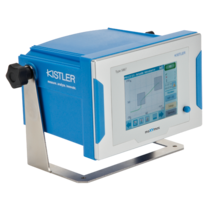
MaXYmos BL Kistler 5867B
Request technical documents for this model
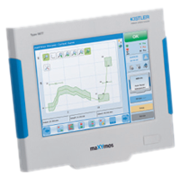
MaXYmos TL Kistler 5877B
Both versions are used for monitoring and archiving data for:
- Bearing installation;
- Drive shaft installation;
- Riveting;
- Screw tightening torque measurement;
- Force/torque quality testing on linear or rotary components
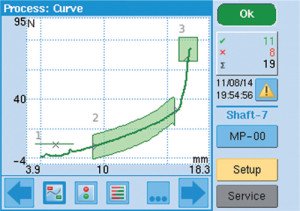
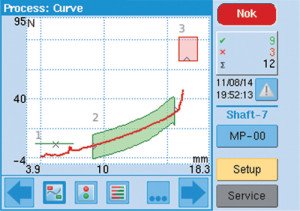
Accessories and complements
Request technical documents for this model
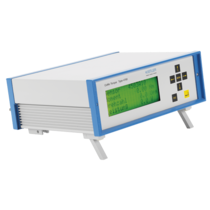
4700B Como torque Kistler
Request technical documents for this model
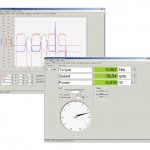
4706A control software
AMPLIFICATION: PIEZOELECTRIC AND STRAIN GAUGE SIGNALS
Signalamplification is essential for measuring mechanical quantities such as force, strain or torque. Charge amplifiers convert the output signal from a piezoelectric sensor to a proportional voltage. These voltage signals are then also used as input variables for monitoring and control processes. To meet industrial needs, Kistler offers a wide range of amplifiers with different designs, number of measuring channels, accuracy, measuring ranges, sensitivity, bandwidth, filter characteristics and scaling and signal processing options.
For piezoelectric sensors
Request technical documents for this model
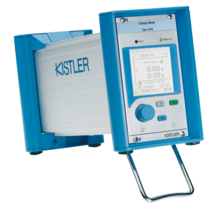
Charge amplifier 5015
Request technical documents for this model
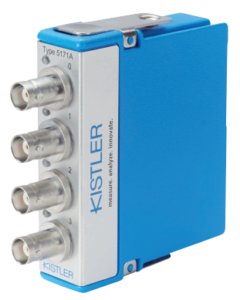
Kistler 5171 A charge amplifier
Request technical documents for this model
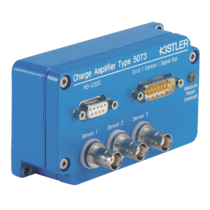
Kistler 5073 charge amplifier
Request technical documents for this model
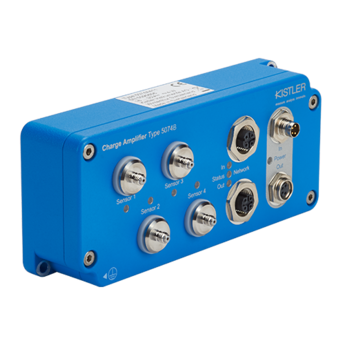
5074B Amplificatore di carica
For strain gauge sensors
Request technical documents for this model
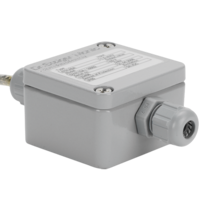
Kistler 4701 strain gauge amplifier
POTENTIOMETERS
They are displacement sensors that can be used in conjunction with the Maxymos and the cell to better monitor the process. The potentiometers measure the stroke with extreme precision.
Request technical documents for this model
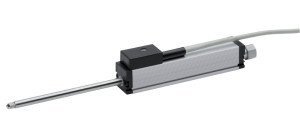
Kistler 2124A Potentiometer
Request technical documents for this model
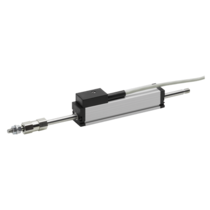
Kistler 2125A Potentiometer
Request technical documents for this model
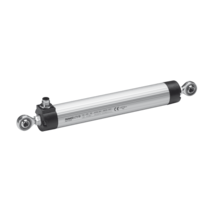
Potentiometer 2121A
Request technical documents for this model
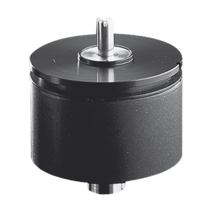
Kistler 2123A Potentiometer
Areas of application
Electric presses, torque transducers, force measurement and acquisition:
- Endothermic engines;
- Electric motors;
- Automotive industry;
- Electrical/electronic industry;
- Mechanical/oleodynamic industry;
- Pharmaceutical/cosmetic industry;
- Machine tools;
- Food industry;
- Laboratories and test bench manufacturers;
- Production lines for different sectors.
KISTLER TECHNOLOGIES
Piezoelectric and strain gauge force transducers
Two operating principles have become dominant in force measurement: Piezoelectric force sensors and strain gauge force transducers. Piezoelectric sensors are active measuring systems, i.e. they do not require external energy to operate. They consist of two crystal disks with a foil electrode between them. When force is applied, an electrical charge is generated that can be measured by a charge amplifier. The charge is proportional to the force applied. Due to their principle of operation, piezoelectric force sensors have an estimated drift of 1 N/minute while the measurement chain is in operation. Since this value remains unchanged irrespective of the measured force, the relative measurement error resulting from the drift is particularly unfavourable when measuring forces over long periods of time.
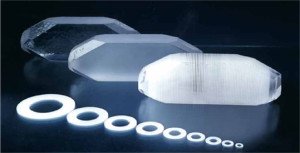
Piezoelectric sensors show very small deflections when force is applied because they offer high stiffness. This results in a high resonance frequency which, in principle, is very favourable for dynamic or quasi-static applications. Piezoelectric sensors can be very compact and are therefore the optimal solution when integration into existing systems is required and for rapid measurements of small forces.
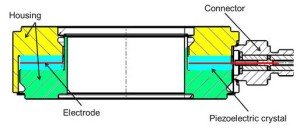
Force transducers Strain gauges are passive measurement systems, i.e. they require external energy to operate. They always comprise a spring element to which force is applied. This force causes minimal deformation of the spring element. Strain gauges installed at appropriate points are lengthened or shortened, and their resistance changes accordingly. At least four strain gauges are connected together to form a Wheatstone bridge circuit. By supplying the measuring bridge with a voltage, the resulting output voltage is proportional to the applied force. These sensors show almost no drift and are therefore particularly suitable for static long-term monitoring tasks such as weighing. The so-called creep (reversible time-dependent change in the output signal that appears when a constant force is applied), is extremely small, as it can be minimised by the appropriate choice of strain gauge design.
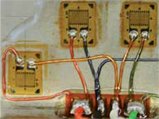